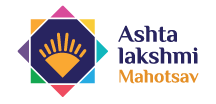
State: Assam (Common in other North-Eastern states as well)
Turmeric, scientifically known as Curcuma longa, is a perennial plant native to South Asia. In the context of natural dyes, turmeric is one of the most ancient and widely used coloring agents, revered for its vivid golden yellow hue. The use of turmeric as a dye dates back thousands of years, traditionally used to color fabrics for religious and ceremonial purposes in India. Its ability to provide a bright and striking color, combined with its natural antiseptic properties, makes it an ideal candidate for handloom and natural dye industries. In the North-East, where sustainable and eco-friendly textile practices are thriving, turmeric dye is increasingly popular for its organic and environmentally conscious properties.
Scan to know more
State: Assam
Assam, known for its rich tea plantations, provides an abundant source of tea waste, which is used innovatively in the production of natural dyes. The use of tea waste as a dye is part of the sustainable practices of utilizing agro-waste to reduce environmental impact. Tea waste dye yields a range of brownish and earthy tones that reflect the natural beauty of the North-Eastern landscape. This natural dyeing process not only enhances the aesthetic appeal of handloom products but also plays a significant role in promoting eco-friendly textile practices across the region.
Scan to know more
State: Manipur, Nagaland, Assam
Onion skin, often discarded as kitchen waste, has been repurposed in the textile industry as a sustainable natural dye. The skin of onions contains a significant amount of quercetin, a plant pigment that produces a warm, earthy range of colors. In the North-Eastern states of India, particularly Manipur, Nagaland, and Assam, onion skin dye has become increasingly popular among artisans who are embracing eco-friendly dyeing techniques. The dye is used to create subtle golden, orange, or brown hues, depending on the concentration and mordant used, which makes it a versatile choice for natural fabric dyeing.
Scan to know more
State: Assam, Manipur, Nagaland
Indigo dye is one of the oldest known natural dyes, and its deep, rich blue color has been used to color textiles for thousands of years. Derived from the Indigofera plant, indigo was once considered so valuable that it was referred to as “blue gold.” In the North-Eastern states of India, such as Assam, Manipur, and Nagaland, the use of indigo dye has deep cultural roots, where it is often used in traditional weaving and handloom industries. Indigo dye’s popularity has persisted through the centuries due to its striking visual appeal and strong historical and cultural significance.
Scan to know more
State: Assam, Manipur, Nagaland
The combination of indigo and onion skin dyes offers an intriguing and versatile approach to natural dyeing. While indigo alone produces a deep, rich blue, combining it with the warm, golden tones of onion skin creates unique shades of olive green. This blend reflects the harmonious use of two natural resources—indigo and onion skins—commonly found in Assam, Manipur, and Nagaland. In these states, artisans have developed innovative dyeing techniques that marry these two colors to create intricate and layered shades, enhancing the visual appeal and cultural significance of their textiles.
Scan to know more
State: Nagaland, Manipur, Assam
Charcoal dye, extracted from burnt wood or organic matter, is one of the most earthy and environmentally conscious dyes used in the textile industry. In the North-Eastern states of Nagaland, Manipur, and Assam, where sustainability and natural resources are central to traditional practices, charcoal dye is commonly employed to create various shades of grey and black. The use of charcoal in dyeing is not just a modern trend but a revival of ancient techniques that relied on readily available natural resources. Artisans in these states are increasingly turning to charcoal dye to create bold, dramatic textiles that align with the growing demand for eco-friendly products.
Scan to know more
State: Assam, Meghalaya
The Gum of the Lac insect (Kerria lacca), more commonly known for its use in producing shellac, is also a valuable source of natural dye. The lac dye produces shades ranging from soft pink to deep crimson, with the most popular being a bush pink color. This dye is particularly significant in Assam and Meghalaya, where traditional handloom artisans have long utilized it to create vibrant textiles. The use of lac insect dye exemplifies the region's resourcefulness, turning a naturally occurring resin into a sustainable and eco-friendly colorant for fabrics.
Scan to know more
State: Manipur, Assam, Arunachal Pradesh
Brazil wood (Caesalpinia echinata) is a tropical hardwood tree known for its use in producing vibrant red dyes. Though the tree is native to South America, the dye it produces has been historically traded and used in many parts of the world, including the North-Eastern states of India. In Manipur, Assam, and Arunachal Pradesh, artisans use Brazil wood dye to create rich shades of red and pink in their textiles. This natural dye is celebrated for its intensity and brilliance, making it a popular choice for traditional garments and handloom products in the region.
Scan to know more
State: Manipur, Assam
The combination of Brazil wood and turmeric dyes creates a stunning saffron hue that blends the rich red of Brazil wood with the vibrant golden yellow of turmeric. In the North-Eastern states of Manipur and Assam, this unique dyeing method is embraced by artisans for its ability to produce a bright, eye-catching color that carries both cultural and spiritual significance. The saffron hue is particularly revered in India, symbolizing purity, energy, and strength. This natural dye combination is often used in traditional garments, adding a layer of beauty and depth to handloom products, reflecting the natural environment and heritage of the region.
Scan to know more
State: Nagaland, Assam
The combination of Brazil wood and charcoal dyes creates an exquisite purple-pink hue that merges the deep red of Brazil wood with the cool, dark tones of charcoal. This blend is particularly valued in Nagaland and Assam, where artisans use it to create textiles that feature rich, complex colors with both visual and cultural significance. The dyeing process highlights the ingenuity of North-Eastern artisans, who skillfully mix natural dyes to produce a palette that reflects the region’s diverse landscapes. The purple-pink shade is prized for its uniqueness and is frequently used in traditional garments and handloom products.
Scan to know more